Stop Biting the Bullet with Unnecessary Magnetic Capacity Checks, Cleaning Headaches, and Downtime
Magnetic Products Inc. (MPI) presents the innovative Wave Magnet™ featuring Intell-I-Mag® technology, specifically designed for capturing ferrous metals in pneumatic conveying systems.
The patented Wave Magnet™ is engineered using the same advanced flow control principles found in Formula 1 race car designs for downforce generation and enhanced cornering speeds, as well as those used in the United States Air Force F-117 Nighthawk for optimal airflow and pressure management, aiding in complex maneuvers and operational efficiency.
The Wave Magnet™ provides a high holding force while reducing flow restrictions compared to traditional pneumatic line magnets, resulting in better flow dynamics and reduced back pressure. The separator is designed to effectively eliminate ferrous contaminants from product streams in pneumatic conveying systems across a range of industries, including food, chemicals, plastics, and pharmaceuticals.
The unit features a self-cleaning design and is equipped with Intell-I-Mag® technology, which eliminates unnecessary shutdowns and blind inspections. It is constructed with 100% stainless steel housing and neodymium rare-earth magnets. It uses a plate magnet-style circuit with three poles and accommodates line sizes of up to four inches in both vertical and horizontal configurations. Its innovative design is streamlined, consisting of a single body with four distinct inlets and outlets for configuration versatility.
The Wave Magnet™ is characterized by a patented wave structure that slows airflow for maximum metal capture and minimal product damage. As the product enters the magnet housing, a diverter channels the flow toward the magnet poles to enhance capture. The diverter creates areas of low flow combined with high gauss, ensuring optimal tramp metal capture.

Industry-Wide Magnetic Separation Pneumatic Conveying Challenges
Magnetic separation is crucial in pneumatic conveying systems for maintaining product purity and protecting processing equipment from metal contamination. Nevertheless, this method encounters multiple challenges that can impact its effectiveness.
System Integration - Integrating magnetic separators into current pneumatic conveying systems without disrupting flow and pressure dynamics is a significant hurdle. The separator must function effectively without causing blockages or pressure drops, necessitating careful design and engineering. The positioning of the magnetic separator must be strategically considered to maximize interaction with the conveyed material while maintaining the pneumatic system's integrity.
Separation Efficiency - A primary challenge of magnetic separation is achieving optimal separation efficiency at high speeds. The presence of fine metal particles, often at a microscopic level, demands the use of powerful magnets. While capturing larger ferrous particles is relatively straightforward, fine contaminants are more difficult to detect. This inefficiency can compromise product quality and risk damage to processing machinery.
Maintenance and Cleanability - Maintenance and cleanability are vital for the ongoing performance of magnetic separators in pneumatic systems. Regular cleaning is necessary to prevent magnet surface saturation, which can reduce their strength and efficacy. However, disassembly and cleaning of magnetic separators can be labor-intensive and may require system downtime, interrupting the production process. Although innovations in self-cleaning magnetic systems exist, they have limited applications.
Material Attrition - Material attrition resulting from the interaction between conveyed particles and the magnetic separator can introduce further complications. The mechanical forces during separation can degrade product quality by producing dust and smaller particles. This issue impacts product integrity and can lead to additional contamination within the system, creating a cycle that undermines overall process efficiency.
Downtime and Product Loss Prevention - Failing to capture metal debris with the magnetic separator can cause considerable downtime, safety hazards, and repair costs. Such neglect may also result in contamination and
recalls, leading to product loss, decreased revenue, and lower profit margins.
Maintaining magnetic integrity is essential in pneumatic conveying systems. If a magnetic separator is dropped or impacted, the internal magnets may fracture, compromising their strength. This risk is heightened during cleaning or maintenance activities, as the separator might be reused without the operator knowing its reduced capabilities. During powder processing, particle accumulation on the magnetic cartridge surface can decrease separation efficiency. In critical cases, the buildup may block the housing, and unnoticed metal saturation could lead to unnecessary production interruptions and costly delays.
Key Features
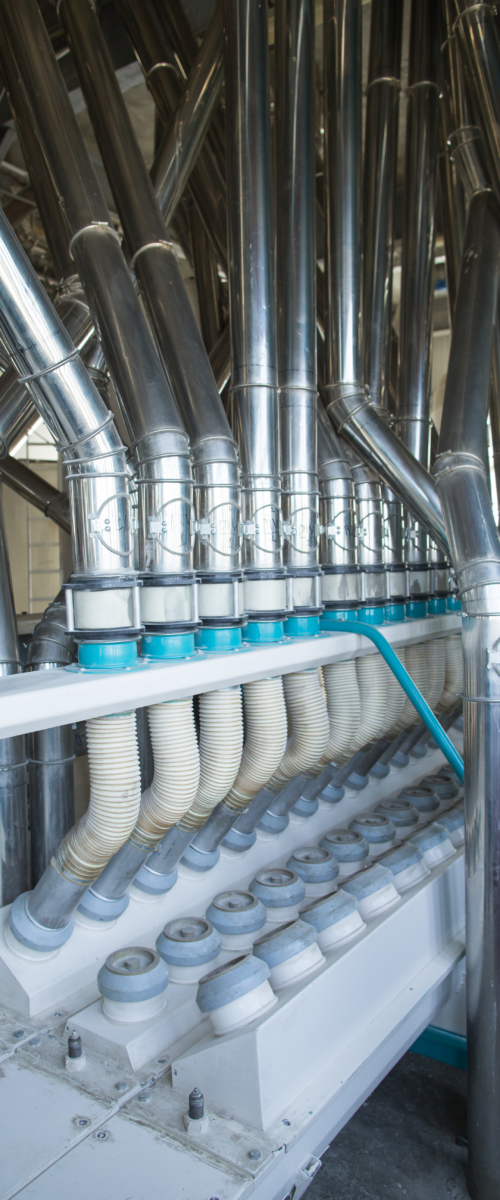
Engineered for Effortless Maintenance - The self-cleaning system guarantees a safer and more automated cleaning process at the touch of a button, minimizing direct contact during maintenance. Featuring an abrasion-resistant face plate and an FDA-approved metal-detectable silicon gasket—streamlining the cleaning of the magnetic separator, reducing downtime, and ensuring product quality and safety downstream.
Equipped with Intell-I-Mag® technology, the system prevents unnecessary shutdowns and repetitive checking processes. Operators are no longer required to halt an entire production line to inspect a magnet that may not need cleaning.
Built for Durability and Versatility - The Wave Magnet™ supports line sizes up to 4 inches in both vertical and horizontal setups. Its innovative and elegant design includes a single body with four distinct inlets and outlets for greater adaptability and versatility. The Wave Magnet™ is built with high-performance neodymium rare-earth magnets and 100% stainless steel.
Aerodynamic Product-Sensitive Design with Maximum Strength and Capture - The curved wave diverter directs the product to flow through the magnetic field, which provides an impressive holding force while utilizing less blower or vacuum capacity, leading to significantly reduced back pressure compared to standard pneumatic line magnets. The three-pole design produces a consistent magnetic field as product flows through the separator. The refined interior angles decrease product impact. The ebb and flow design gently moves the product, while strong neodymium rare-earth magnets effectively capture any tramp metal in the product stream. This
configuration enhances exposure to the magnetic field, minimizing friction and wear on delicate or fragile product streams. Laboratory tests show that the Wave’s advanced circuit design maintains metal retention until it interferes with the product flow.
Optimal Flow Efficiency and Pressure Distribution - It delivers a strong holding force while minimizing flow impact compared to conventional pneumatic line magnets, enhancing flow dynamics and reducing back pressure. This ensures optimal product capture. The patented wave design effectively slows airflow, facilitating the most efficient separation. The product is divided into two diverter chambers, directing the product flow over three poles per side (a total of six). Each chamber, along with the diverter, includes two reach-out poles and one holding pole with a higher gauss to maintain product retention.
Intell-I-Mag®: Sensor-Enabled Intelligent Separation - Intell-I-Mag® is a technology platform that pairs sensors within a magnetic separator with an app or computer-based dashboard to measure and report magnet how much metal is on your magnet in real time. This patented system is the first and only magnetic separation technology of its kind. MPI’s Wave Magnet™ comes Intell-I-Mag®-Ready as standard, so it’s easy and cost-effective to enable Intell-I-Mag® at any time.
Proven Benefit and ROI
Intell-I-Mag® is patented technology exclusively available from Magnetic Products, Inc. Magnetic Product Inc.’s intelligent magnet design self-monitors its performance in real time 24/7 to maintain peak performance.
The Intell-I-Mag® Controller monitors tramp metal saturation levels on the working surface of the magnetic separator in real time. The magnetic separator has sensors embedded into the separator that measure the strength of the magnetic field. These sensors report data collected in real time to the Intell-I-Mag® Controller. The controller can be programmed to automatically alert operators to clean the magnetic separator remotely when it reaches industry-designated saturation levels.
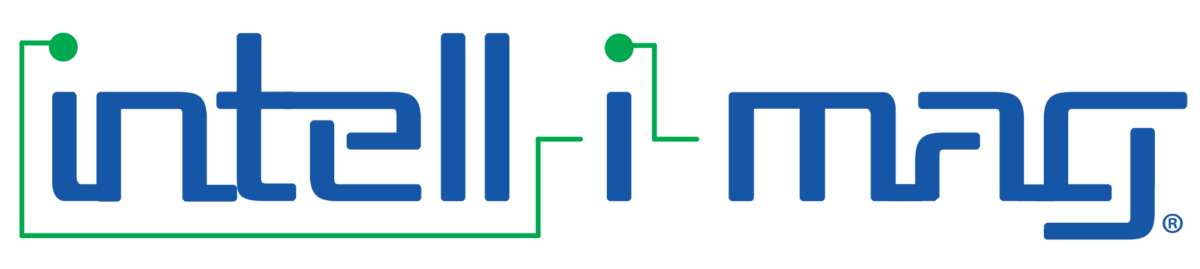
Intell-I-Mag® is engineered with versatility and compatibility in mind:
- The Intell-I-Mag® Controller and App monitor within a 25m (80ft.) radius.
- The Intell-I-Mag® system can be rated NEMA 4X for wet applications or where high-pressure washdown is required.
- Suitable for high-temperature applications. Good for operating temperatures up to 105C (221F). With intermittent temperatures < 30 seconds for cleaning up to 125C (257F).
- The permanent magnet will continue to capture tramp metal if the controller is disconnected or not working for any reason.
- Intell-I-Mag® can be added to any self-clean unit at any time.
Before Intell-I-Mag®, there was no way for an operator to know the saturation level of their magnetic separator other than by shutting down the production line to check.
Intell-I-Mag® changes that. One Intell-I-Mag® early-adopter was able to reduce their total number of magnet cleaning stoppages by more than 2/3rds in the first year of piloting the system, and, as a result, reduced downtime and human resource expenditures required to maintain their magnetic separators, increasing revenue by more than $1.5M. That’s the power of an intelligent magnet.
In addition to capacity alerts, Intell-I-Mag® automatically collects and logs cleaning history and collection trends, letting the operator – and QA/QC personnel – know when it was cleaned, when there was a spike in saturation, and what events – for example, deliveries – were the most significant
contributors to metal in the product stream. The improved production quality and efficiency won Intell-I-Mag® Best of Show at The International Association of Operative Millers (IAOM) and Best in Supplier Plant Efficiency at the International Baking Industry Exposition (IBIE) in its inaugural year.
Magnetic Products, Inc is Leading an Evolution in Metal Control with Intell-I-Mag®’s disruptive technology
- Improved confidence that the magnetic separator is performing at peak, capturing the most challenging tramp metal in, including work-hardened stainless steel.
- Assurance that vendors are not unloading tramp metal into your
facility at receiving locations. - Earlier metal detection, which protects equipment throughout the production line.
- Reduced downtime by only shutting down a line to clean a magnet when needed.
- Increased equipment efficiency and monitoring reduces maintenance costs.
- Prolonged magnetic viability and protection against degradation with the built-in temperature monitoring.
- Optimized labor productivity - employees can perform duties besides checking magnets.
- Confidence that plant operators have cleaned the magnet through the data validation of the Intell-I-Mag® sensors.
- Decreased staff hours required for maintaining magnetic separators.
- Automated QC data collection and improved data quality for internal QA programs, auditors, and customers.
- Elimination of paper cleaning records through automatic data logging.
Industry Legacy
Magnetic Products Inc. (MPI) has revolutionized the industry for 43 years with its unwavering commitment to R&D and the core value of high-performance engineering by introducing the world’s first quick-clean permanent magnetic separators with the self-cleaning chute magnet in 1983, the patented magnetic can-laner conveyor in 1989, and the patented reciprocating drawer magnet in 1991.
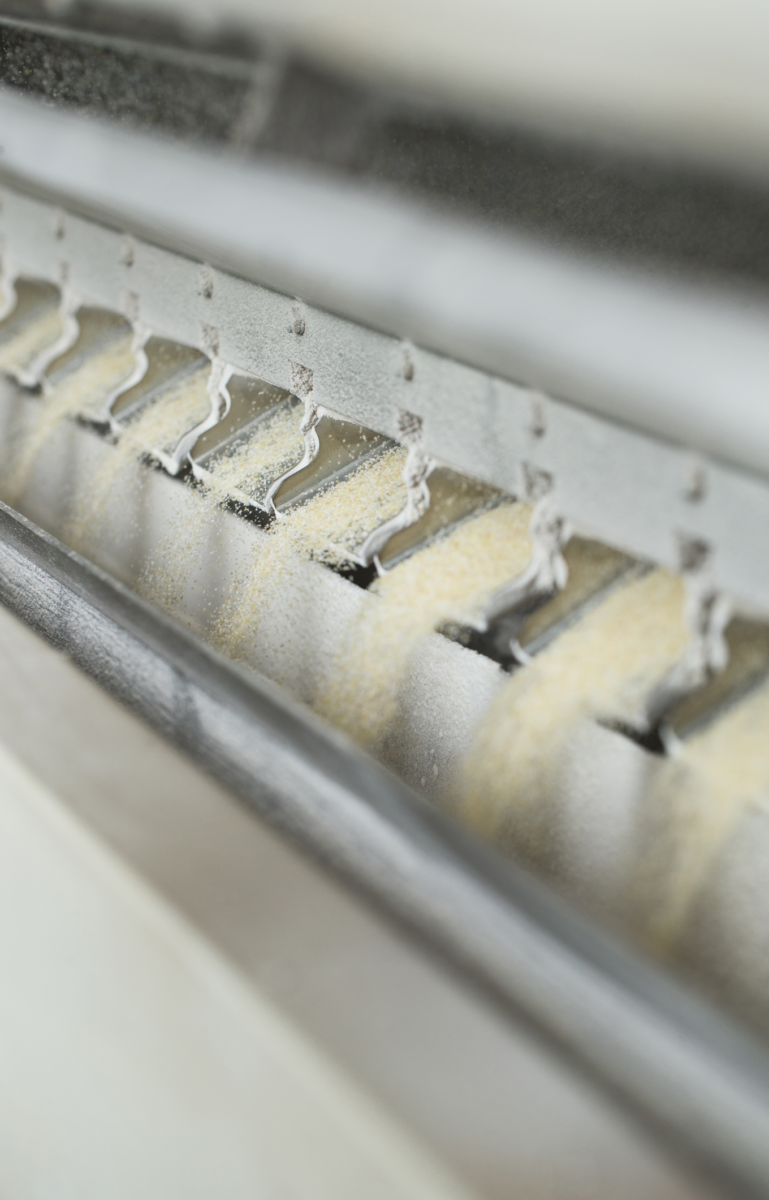
Magnetic Products, Inc. (MPI) is a Michigan-based OEM focused on developing and manufacturing cutting-edge magnetic separation and material handling equipment for food and bulk material processors, metal stamping companies, and related industries.
Combining advanced manufacturing with over 40 years of industry experience, the company is pioneering new sensor-enabled product lines to complement its proprietary shakers and conveyor systems. In addition, MPI conducts audits on metal control systems and sets the industry standard for system maintenance requirements.