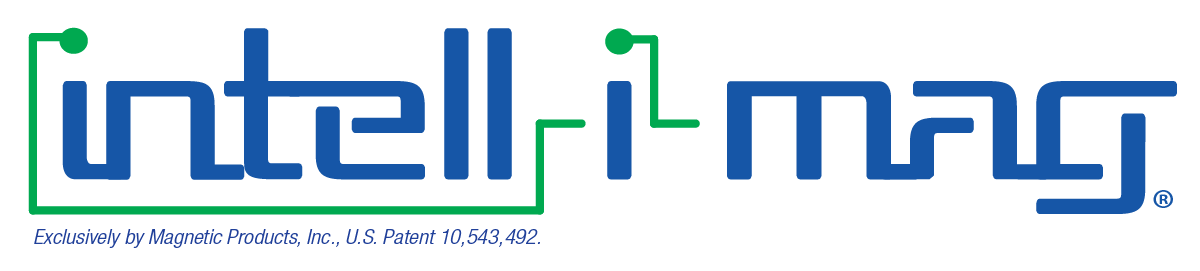
Intelligent Metal Control – Solving A 150 Year Old Problem With Technology
Intelligent magnetic separation addresses a problem faced by the industry for more than 150 years – operators must shut down an entire processing line to check a magnet that may, or may not, need to be cleaned. Intell-I-Mag® is a technology platform that pairs sensors within a magnetic separator with an app or computer-based dashboard that alerts an operator when the magnet has reached their designated level of saturation. This allows the operator to assess a magnet’s need for cleaning through the dashboard, without shutting down the processing line. This eliminates unnecessary maintenance stoppages and reduces lost production time, while offering the same protection against metal contamination as traditional magnetic separators.
Proven ROI – $1.5M Saved in One Year
When 4 Sisters and a Rice Farm in Louisiana added Intell-I-Mag® to their Kennedy Rice Mill, they reduced magnet maintenance-related downtime and increased throughput and, as a result, earned more than $1.5M in additional revenue in one year of use. The Mill reduced the total number of magnet cleaning stoppages by 2/3rds from once a day to once every three days without increasing their risk for metal contamination.
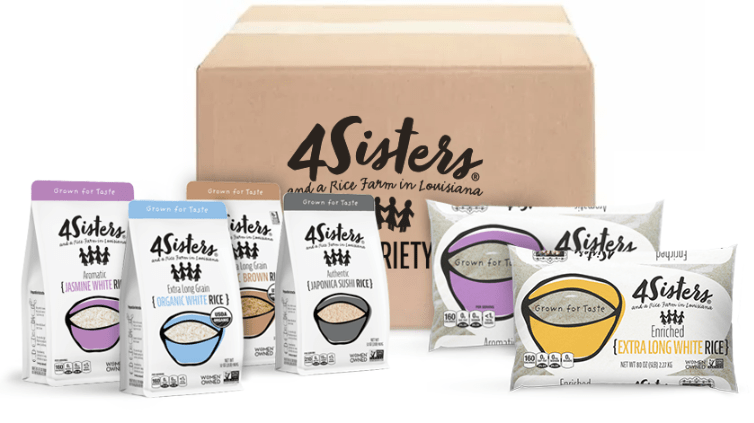
Straight From the Customer
“It’s going to make us a tremendous amount of money by reducing the frequency of magnet checks.”
~ Matt Fowler, Quality & Food Safety Director, 4 Sisters and a Rice Farm in Louisiana
Key Benefits
- Improved confidence that magnetic separator is operating at peak performance
- Delivery monitoring to ensure vendors are not unloading metal into the facility
- Earlier metal detection, which protects downstream processing equipment
- Reduced downtime by only shutting down a line to clean a magnet when it is saturated
- Increased equipment efficient and monitoring reduces maintenance costs
- Automated QC data collection and improved data quality
- Prolonged magnetic viability and protection against degradation with built-in overheating alert sensor
- Optimized labor productivity – operators can perform duties other than checking magnets
- Confidence in cleaning logs through data validation of the Intell-I-Mag® sensors
- Elimination of paper cleaning records through automatic data logging
Built for Versatility and Compatibility
The Intell-I-Mag® platform monitors tramp metal saturation on the working surface of the magnetic separator in real time with embedded sensors that continuously measure the strength of the magnetic field. These sensors report data to a hardwired control box near the separator. That data is then transmitted via bluetooth to a mobile app or through a direct connection with the internal plant control system – alerting the operator that when the magnet requires cleaning. Even without access to the digital platform, an operator can view the built-in LED indicator light to know if the magnet is working at peak, is filling up, or needs immediate attention.
Flexible Solutions
- Available on drawer, plate, chute, and pneumatic inline plate magnets, as well as magnetic rotary feeders
- Can be rated NEMA 4X for wet applications or where high-pressure washdown is required
- Suitable for high-temperature applications – up to 105C (221F) with intermittent temperatures (<30 seconds) up to 125C (257F)
- Can be added to most compatible models at any time
- Permanent magnet continues to function even if the Intell-I-Mag® platform is offline
Intell-I-Mag® Awards
![]() |
![]() |
Best of Show |
Supplier Plant Efficiency 2022 IBIE BEST in Baking Program |
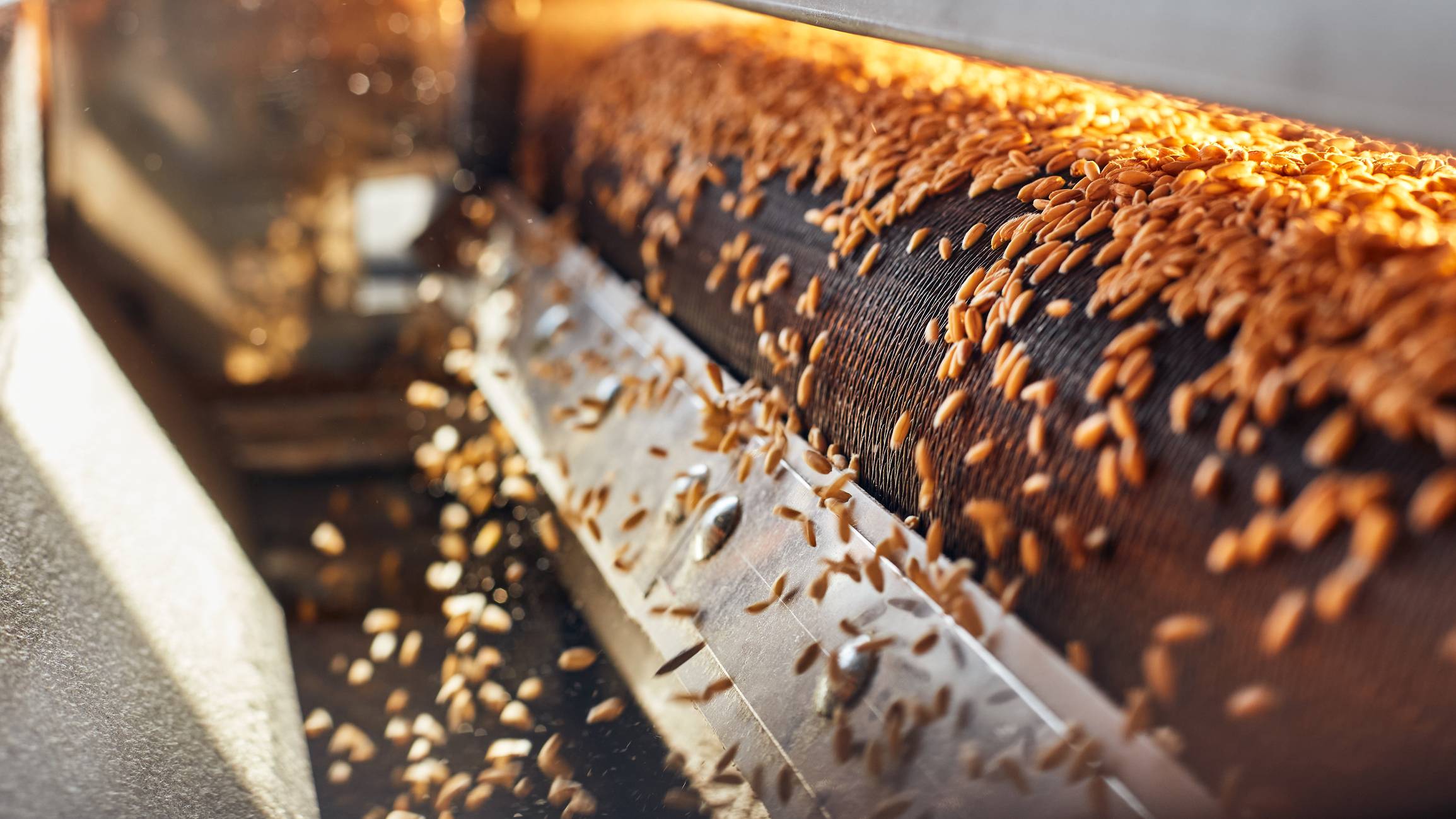